Abstract: In the process of CNC machining, burr generation is a significant factor affecting the quality of machined parts. This article analyzes the causes of burrs in CNC machining parts, discusses the key techniques for deburring, and proposes corresponding solutions.
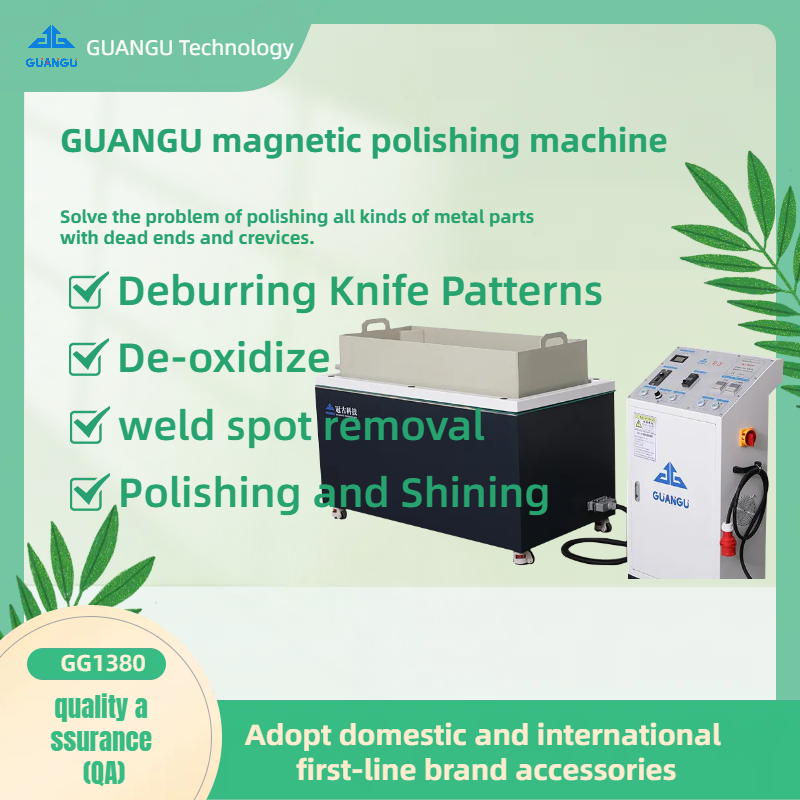
Introduction
With the rapid development of the manufacturing industry, CNC machining technology has been widely applied in various fields such as aerospace, automotive, and mold making. In the CNC machining process, burr generation has always been a key factor affecting the quality of machining. Burrs not only reduce the surface quality of parts but can also lead to wear and fatigue issues during usage. Therefore, studying deburring techniques for CNC machining parts has important practical significance.
Causes of Burr Generation
- Tool wear: During the CNC machining process, the friction between the tool and the workpiece leads to tool wear, resulting in burr generation.
- Tool parameter setting: Improper setting of tool geometry parameters and cutting parameters may cause burr generation.
- Workpiece material: The hardness and toughness of the workpiece material affect the cutting performance of the tool, thereby influencing burr generation.
- Machining environment: During the machining process, coolants and chips can affect the cutting performance of the tool, leading to burr generation.
Key Techniques for Deburring in CNC Machining Parts
- Selecting suitable tools: Choosing tools with good cutting performance based on workpiece material and processing requirements is the premise for reducing burr generation.
- Setting tool parameters reasonably: Reasonably setting tool geometry parameters and cutting parameters can improve the cutting performance of the tool and reduce burr generation.
- Optimizing machining process: By optimizing the machining process, such as using appropriate cutting speed, feed rate, and cutting depth, the probability of burr generation can be reduced.
- Tool compensation technology: Using tool compensation technology can adjust the cutting position of the tool in real-time, reducing burr generation.
- Selection and use of cutting fluids: Reasonably selecting and using cutting fluids can reduce the friction between the tool and the workpiece, thereby reducing burr generation.
- Post-processing: After the CNC machining is completed, post-processing methods such as grinding and polishing can remove burrs and improve the surface quality of the parts.
Conclusion-Deburring in CNC Machining Parts
Deburring in CNC machining parts is a critical step to improve machining quality. By analyzing the causes of burr generation, discussing key deburring techniques, and proposing corresponding solutions, the impact of burrs on machining quality can be effectively reduced. At the same time, machining enterprises should continuously optimize the machining process and improve the technical level of machining to enhance the quality of machined parts.
يجب أنت تكون مسجل الدخول لتضيف تعليقاً.